Zirconia was introduced to the market in the 2000s. It was the strongest ceramic ever put on market at the time and introduced as a framework material only. Framework materials were very opaque, available in white discs only, and dipping was necessary for stain and glazing. Today, there are pre-shaded discs, multi-layered discs, and different strengths and translucency. White discs are ideal for small to medium sized labs because they can have lower inventory and have control over customizing esthetics. Pre-shaded zirconia is ideal for labs that have difficulty achieving the desired shade after sintering, struggle with sorting units by shade, or have labor consistency issues or multiple shifts. You’ll have a larger inventory when working with pre-shaded zirconia. The material is monochromatic and more consistent and predictable, and your batches will be smaller when milling which means if you only have one mill, adding another might be useful to you. Multi-layered discs are like pre-shaded but with higher esthetics.
Zirconia discs can also be categorized by how they’re manufactured, primarily in two different ways; axial pressed or isostatically pressed. Axial pressed discs are made by a die. A formulated powder is loaded into the die and the powder is then pressed at a minimum 30K PSI. It’s then sintered at 900 to 1000C with a 3.5 day cycle. Some zirconia is sintered hotter resulting in a harder disc and others are sintered cooler resulting in softer discs that may be more susceptible to chipping. After the discs are sintered, they are milled to their final shape and a shoulder is added. Cold isostatic pressing or CIP means the powder goes through an axial pressed method and then several discs are placed in a flexible vessel. This vessel is placed in water and the water is put under load. Discs are loaded evenly 360 degrees in all directions. After, they are sintered similarly to the axial pressed discs. These discs are homogeneous and have the same density throughout.
Because there are so many different types of zirconia on the market, it can be confusing when choosing each for the many different types of restorations your lab is producing. We recommend categorizing zirconia into 3 major categories based on strength and translucency. The first is High Strength (HS) which means its flexural strength is 1,200 MPa or more. The second is High Translucent (HT) which means it has a flexural strength of 1,100 MPa. Lastly, the first category is Super Translucent (ST) in which its flexural strength is about 600 to 700 MPa.
Each type of zirconia has a special place in your lab! The chart below can help you decide when you should use each type of zirconia for what type of restoration you’re fabricating. The left column are factors that you should consider when determining which zirconia is a good fit for a specific case including translucency, the material’s ability to cover a dark stump, if you’re working on a bridge application or not, the material’s ability to be layered or micro layered, or if you want to work with a full contour monolithic material or not.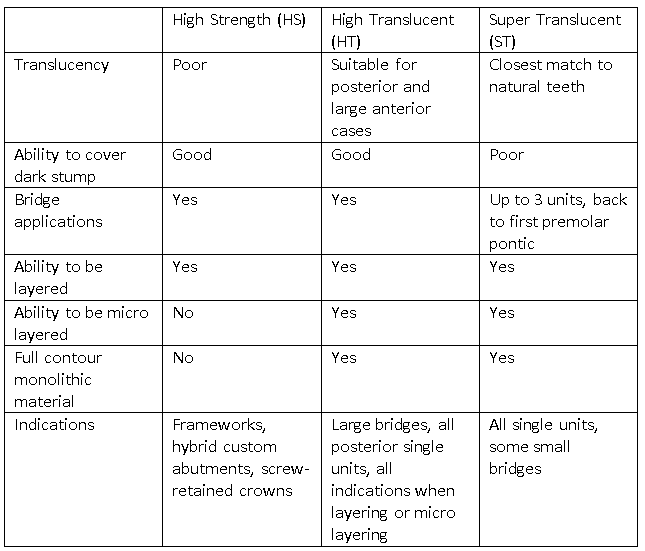
*This is merely a recommended guide. All bridgework must have adequate connector volume and cantilevers would only be considered when using HS or HT with the exception of maybe a small lateral incisor.
When deciding what type of zirconia you want to use in your lab, you should always choose one that’s easy to use, chip resistant, has a consistent manufacturing process, and is cost effective but not necessarily the cheapest because it should provide the greatest value to your customer, and lastly, you can get product support whenever you need it.
Thanks for reading,
Your Zirlux Team